Executive Secretary
Conferencia Internacional de Producción y Uso Sostenible del Cemento y Hormigón
This work describes the production process for the first formulation of a limestone-calcined clay cement in Guatemala, with a total production of 160 metric tons of cement. After reviewing more than 10 possible sites for extraction of clays at several regions, that could accomplish the criteria for usage as an activated clay material, a 67% of kaolin content material was finally selected, on a location around 50 Km of our cement factory. With the selected material, a theoretical formulation by weight was defined of 48% clinker, 30% calcined clay, 17% limestone and 5% gypsum, the process began with the thermal activation of the clay, by passing 125 tons of raw material by a rotary kiln at 750-850°C, temperature control was possible due a series of control points using a thermal imaging camera, the activation process was controlled by X-Ray Diffraction, looking for the reduction of the signal for kaolin type clays, obtaining 90 tons of activated material. The cement produced had a 48% of clinker content verified by XRD, around 12% lower than any general use cement produced in the country. This cement was tested for strength development, setting time, hydration heat, and alkali-silica reactivity showing a very good performance. No critical difference was perceived between the concrete produced with the new cement and one with 83% of clinker with similar strength performance at 28 days evaluated by ASTM C39. The mortar, developed a superior strength compared to the national normative for a general usage cement ASTM C1157.
This work describes the production process for the first formulation of a limestone-calcined clay cement in Guatemala, with a total production of 160 metric tons of cement. After reviewing more than 10 possible sites for extraction of clays at several regions, that could accomplish the criteria for usage as an activated clay material, a 67% of kaolin content material was finally selected, on a location around 50 Km of our cement factory. With the selected material, a theoretical formulation by weight was defined of 48% clinker, 30% calcined clay, 17% limestone and 5% gypsum, the process began with the thermal activation of the clay, by passing 125 tons of raw material by a rotary kiln at 750-850°C, temperature control was possible due a series of control points using a thermal imaging camera, the activation process was controlled by X-Ray Diffraction, looking for the reduction of the signal for kaolin type clays, obtaining 90 tons of activated material. The cement produced had a 48% of clinker content verified by XRD, around 12% lower than any general use cement produced in the country. This cement was tested for strength development, setting time, hydration heat, and alkali-silica reactivity showing a very good performance. No critical difference was perceived between the concrete produced with the new cement and one with 83% of clinker with similar strength performance at 28 days evaluated by ASTM C39. The mortar, developed a superior strength compared to the national normative for a general usage cement ASTM C1157.
Sobre el ponente
S. Torres
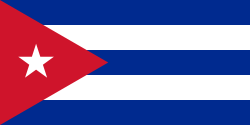