Executive Secretary
10th International Conference of Mechanical Engineering
COMEC 2019
Abstract
In comparison to machining with geometrically defined cutting edges, grinding manifests clear procedural differences that effect the machinability of the materials. Grinding is achieved by means of a number of individual grit engagements. During grinding is increased amount of friction and deformation work, from which results a higher conversion of heat flow in the process. The paper presents the modeling of the contact temperature between the wheel and the workpiece during surface grinding. The measurement of the contact temperature during grinding was performed firstly by using an artificial thermocouple that was incorporated into the workpiece, using a developed acquisition system connected with the computer. Measurement of values was carried out by factorial plan of the experiment. Input experimental data were elements of the cutting regime: table speed, transverse shift and grinding depth and output data contact temperature. The processing of data using the response surface methodology determines the adequate dependence in the form of the power function and the estimated influence of individual input factors. Then modeling was done using artificial neural networks. Finally, a comparison of the calculated values with the both models was performed and the better model of surface grinding process was adopted.
Resumen
In comparison to machining with geometrically defined cutting edges, grinding manifests clear procedural differences that effect the machinability of the materials. Grinding is achieved by means of a number of individual grit engagements. During grinding is increased amount of friction and deformation work, from which results a higher conversion of heat flow in the process. The paper presents the modeling of the contact temperature between the wheel and the workpiece during surface grinding. The measurement of the contact temperature during grinding was performed firstly by using an artificial thermocouple that was incorporated into the workpiece, using a developed acquisition system connected with the computer. Measurement of values was carried out by factorial plan of the experiment. Input experimental data were elements of the cutting regime: table speed, transverse shift and grinding depth and output data contact temperature. The processing of data using the response surface methodology determines the adequate dependence in the form of the power function and the estimated influence of individual input factors. Then modeling was done using artificial neural networks. Finally, a comparison of the calculated values with the both models was performed and the better model of surface grinding process was adopted.
About The Speaker
Pavel Kovač
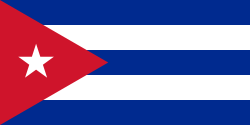