Executive Secretary
VIII International Symposium on Chemistry and Pharmaceutical Sciences
SIIQ
XIII Conference "Chemical Engineering: Development, potentials and challenges"
Abstract
This work analyzed the fermentation and distillation stages of the process of obtaining extrafine alcohol at the "Heriberto Duquesne" distillery. A simple lattice experimental design was used to evaluate the impact of secondary juice, filter juice and final molasses on the alcohol content and fermentation efficiency. The best results were obtained in the experiments using filter juice and molasses, reaching efficiency at the 85% stage and must fermented at 6oGL. The results were statistically processed, allowing the determination of the model that describes the behavior of both parameters. By means of the material and energy balances, the steam and cooling water consumption in each column was calculated, obtaining a steam consumption rate of 0.566 t/hL from the steam generator, as well as a cooling water rate of 13.34 m3/hL alcohol. To achieve savings in steam consumption at this stage, three boilers were sized for the washing, recovery and demethylizing columns, reducing the steam and water consumption rates to 0.46 t steam/hL and 8.63 m3 of water/hL, respectively. The proposed investment and the savings in water and fuel consumption made it possible to achieve positive dynamic profitability indicators.
Resumen
El presente trabajo analizó las etapas de fermentación y destilación del proceso de obtención de alcohol extrafino en la destilería “Heriberto Duquesne”. En la fermentación se desarrolló un diseño experimental del tipo enrejado simple evaluando el impacto del jugo secundario, jugo de los filtros y miel final en el grado alcohólico y la eficiencia en la fermentación. Los mejores resultados se obtuvieron en los experimentos que se utilizó jugo de los filtros y miel, alcanzando una eficiencia en la etapa de 85% y mosto fermentado con 6oGL. Los resultados se procesaron estadísticamente, permitiendo determinar el modelo que describe el comportamiento de ambos parámetros. Mediante los balances de materiales y energía se calcularon los consumos de vapor y agua de enfriamiento en cada columna, obteniendo un índice de consumo de vapor de 0,566 t/hL provenientes del generador de vapor, así como un índice de agua de enfriamiento de 13,34 m3/hL alcohol. Para lograr un ahorro en el consumo de vapor en esta etapa se dimensionaron tres ebullidores para las columnas lavadora, recuperadora y desmetilizadora, logrando reducir los índices de consumo para el vapor y el agua hasta valores de 0,46 t vapor/hL y 8,63 m3 de agua/hL respectivamente. La inversión propuesta y el ahorro del consumo de agua y combustible permitieron alcanzar indicadores dinámicos de rentabilidad positivos.
About The Speaker
Ana Celia de Armas Martínez
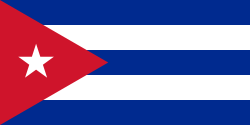
Discussion